Shortage of building supplies is a setback many are facing
With Brexit settling in and the pandemic hitting the UK in March 2020, they both had a global impact in many different areas. They have now formed conditions for the low supply and high costs, which have been affected by costly international shipping charges.
One of the industries that are seeing huge demand, which businesses can’t keep up with, is building materials suppliers. The summer of 2021 is the peak of this crisis. Many suppliers are finding it difficult to manufacture and distribute their stock.
As a result of this, not only are supplies on the low, but the prices are rising at an escalating pace, as well. One particular example that showed a staggering price increase was timber, which skyrocketed by 120%.
How are businesses handling the huge demand?
One of the key things to do is be up to date with the government’s guidance, which is updated regularly and can ensure that businesses can expect the unexpected. This is the best course of action since the construction industry is probably going to continue facing issues in the autumn and winter of 2021. Businesses should try to think ahead, identify and cope with future risks.
Another way to tackle the crisis is to reevaluate the business’ processes regarding cash flow, quality, contracts and timeframes. This way, the budget and volume of work can become manageable. It will also help the business be ready for once things return to normal.
Reassessing the pool of subcontractors and branching out to new suppliers can also be quite beneficial. It’s crucial to connect and cooperate with the supply chain to find out if reviewing the contract terms or any further renegotiations, is needed.
It’s best to think ahead and consider how any issues the supply chain faces can affect your business financially.
The main reasons behind low building materials supplies
The starting point of this crisis began back in 2020 when many families chose to invest in their homes the money they couldn’t spend on holidays abroad due to lockdown.
This June, construction manufacturers reached a peak in activity, which hasn’t been seen since 1997. The issue is that this type of demand isn’t being met by suppliers, which has resulted in delivery times being longer than usual. A delivery that would’ve taken a week or two is now being extended to 6 weeks or even longer.
Another common crisis that is happening across the whole of the UK is the lack of lorry drivers. Companies have been struggling to find and recruit additional delivery drivers across many industries. This situation, in turn, has resulted in longer shipping times.
What is affecting the shortage of building materials is that globally there is a deficit of raw materials. External factors such as global demand and factories closing outside of the UK have affected this. These types of circumstances continue to slow down the manufacturing process of products. These include renders, adhesives, paints and other insulation materials.
What is the current situation with JUB’s renders and external insulation systems?
Due to the long-term relationships we have built with raw material suppliers, JUB has been able to maintain stock levels and material supplies.
“To date, our raw materials supply has been fluid, which hasn’t led to any disruption in our production plan without having any delays in supplying our customers.”
-Steve Franklin, Managing Partner, JUB Systems Ltd.
As of currently, we are handling the demand in supply. We will continue to plan for the future utilising this process, which reflects on the rapid growth of the company.
The post Shortage of building supplies is a setback many are facing appeared first on JUB Render Systems.
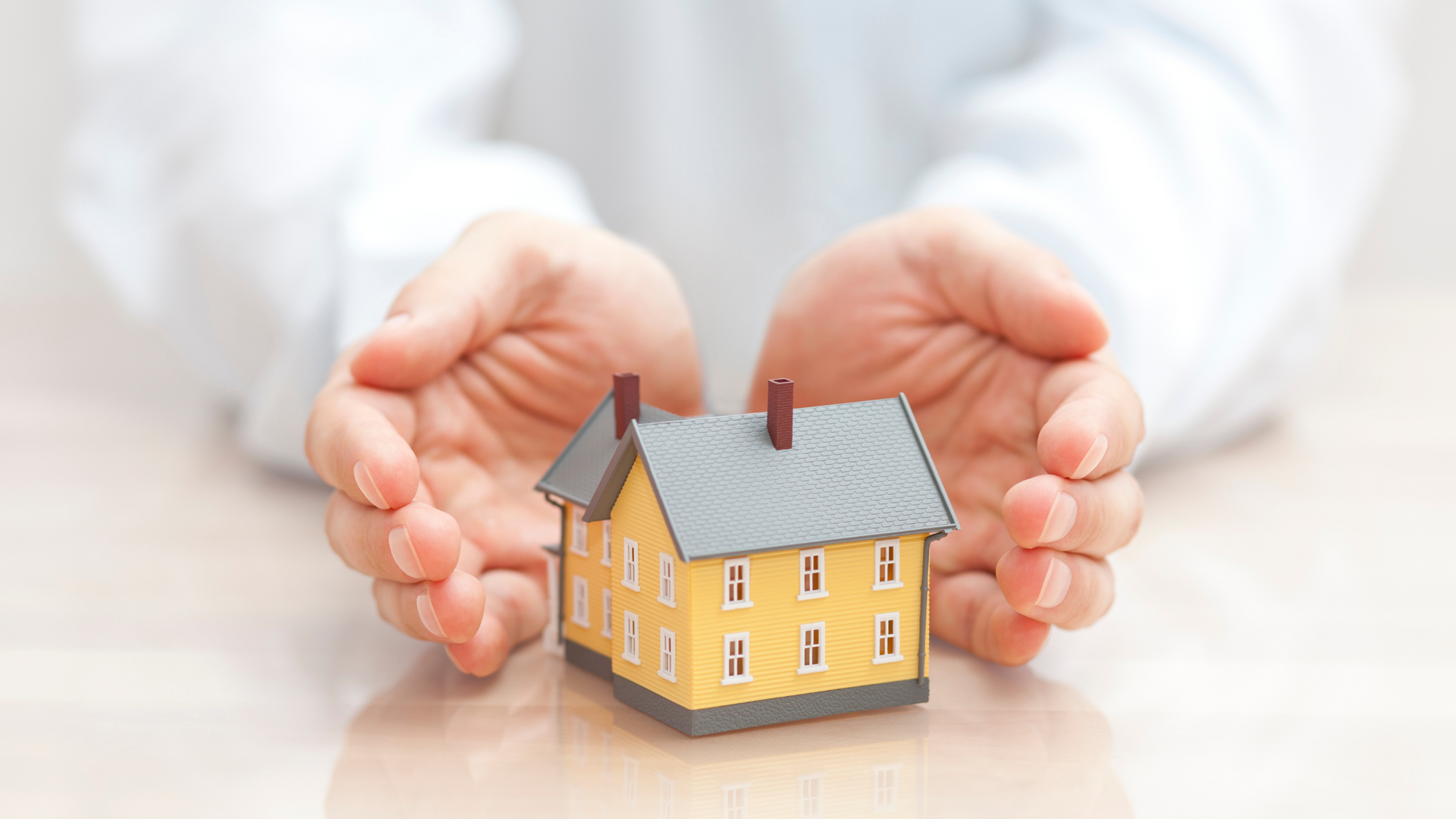
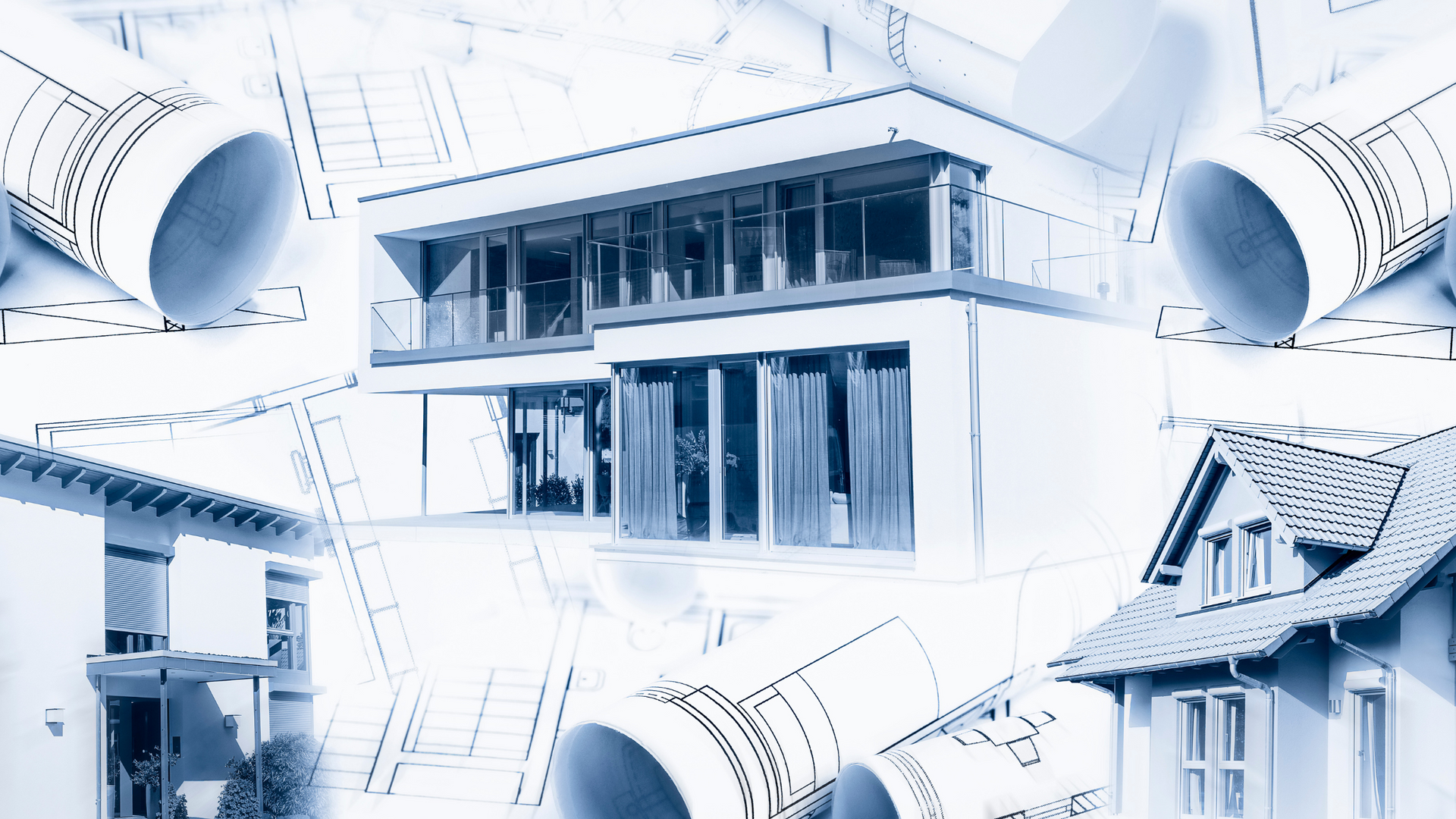
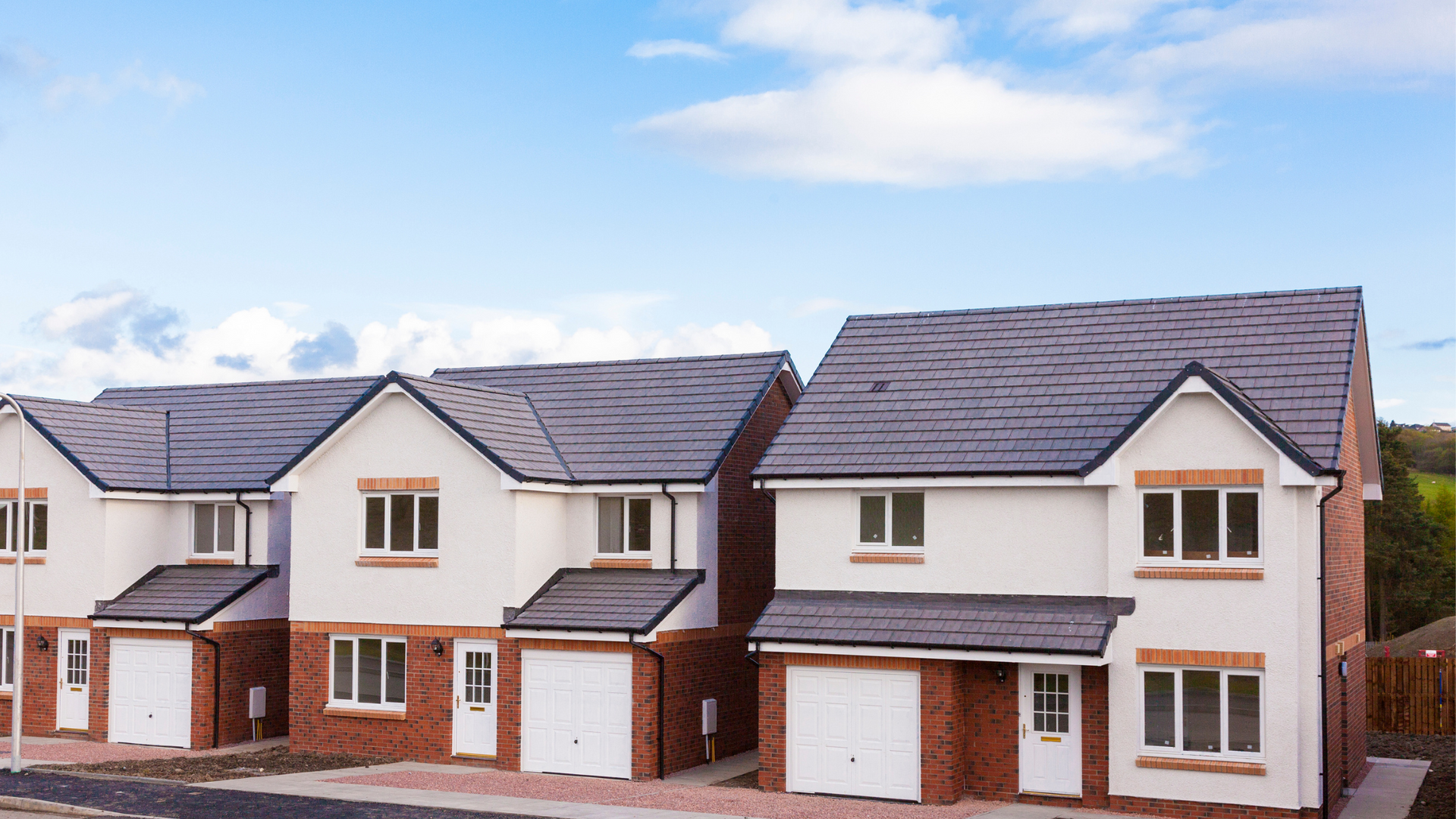
Why Silicone Render is the Best Choice for a Property’s Exterior: Benefits, Application & Aesthetics
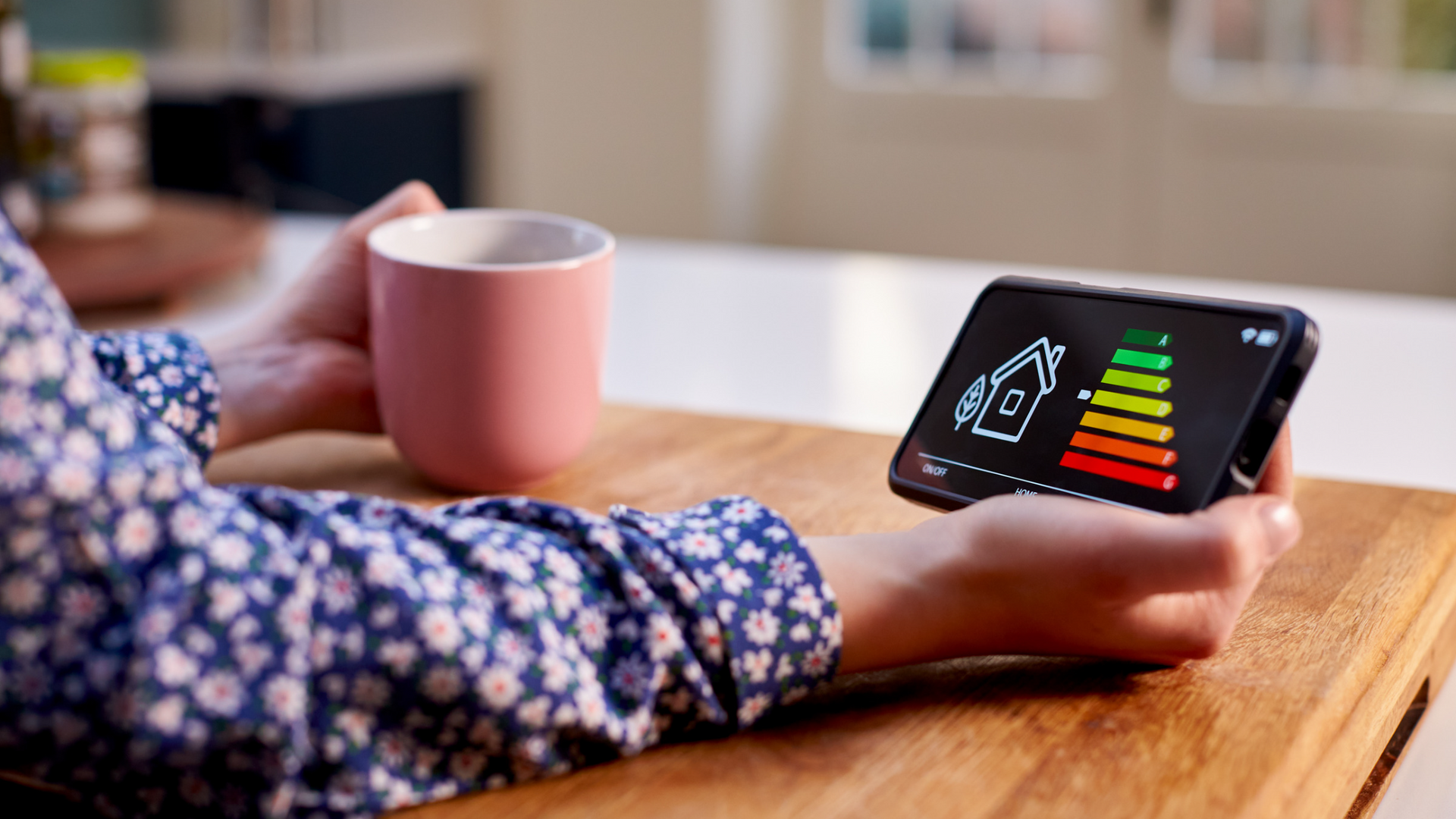
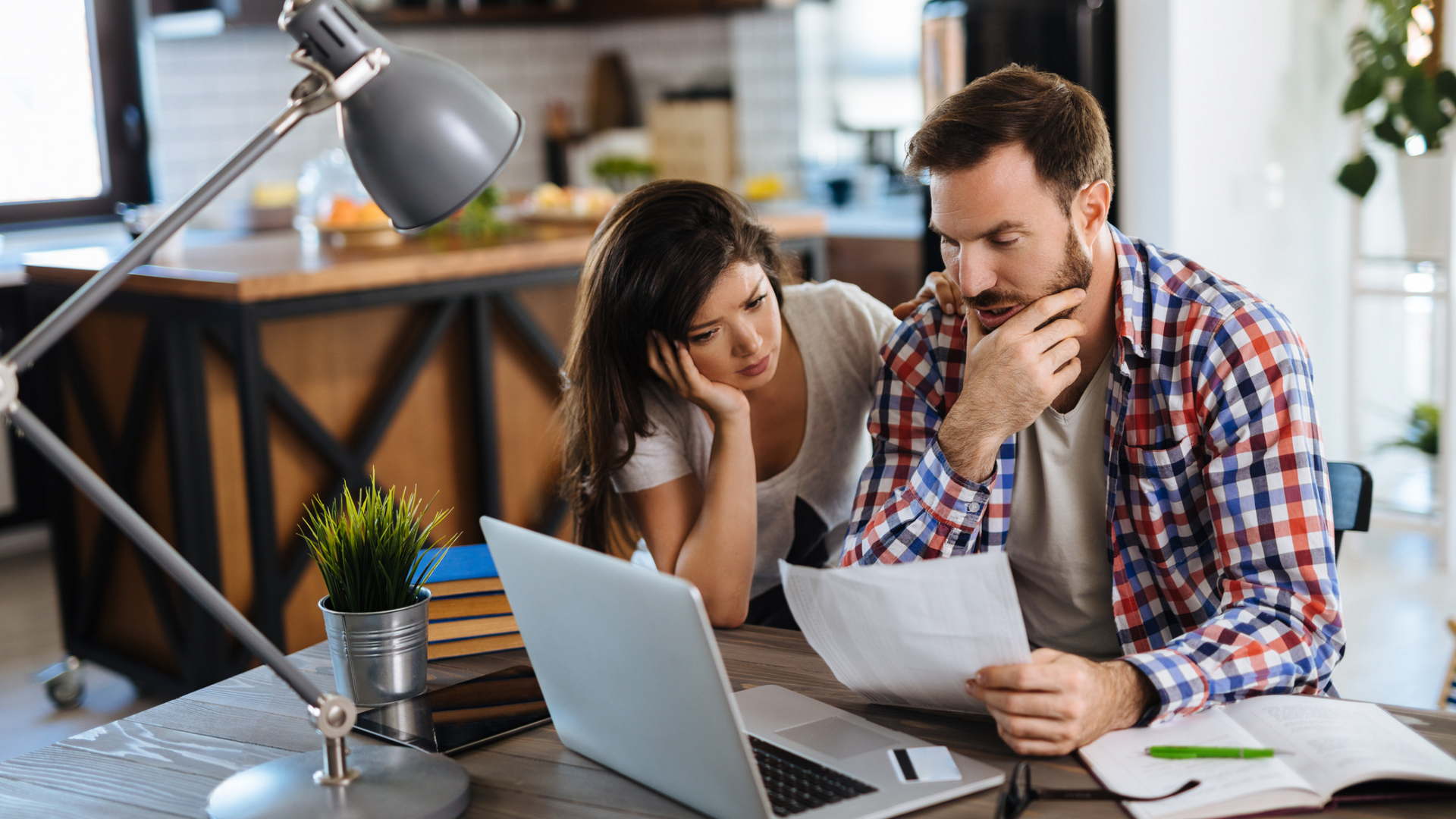
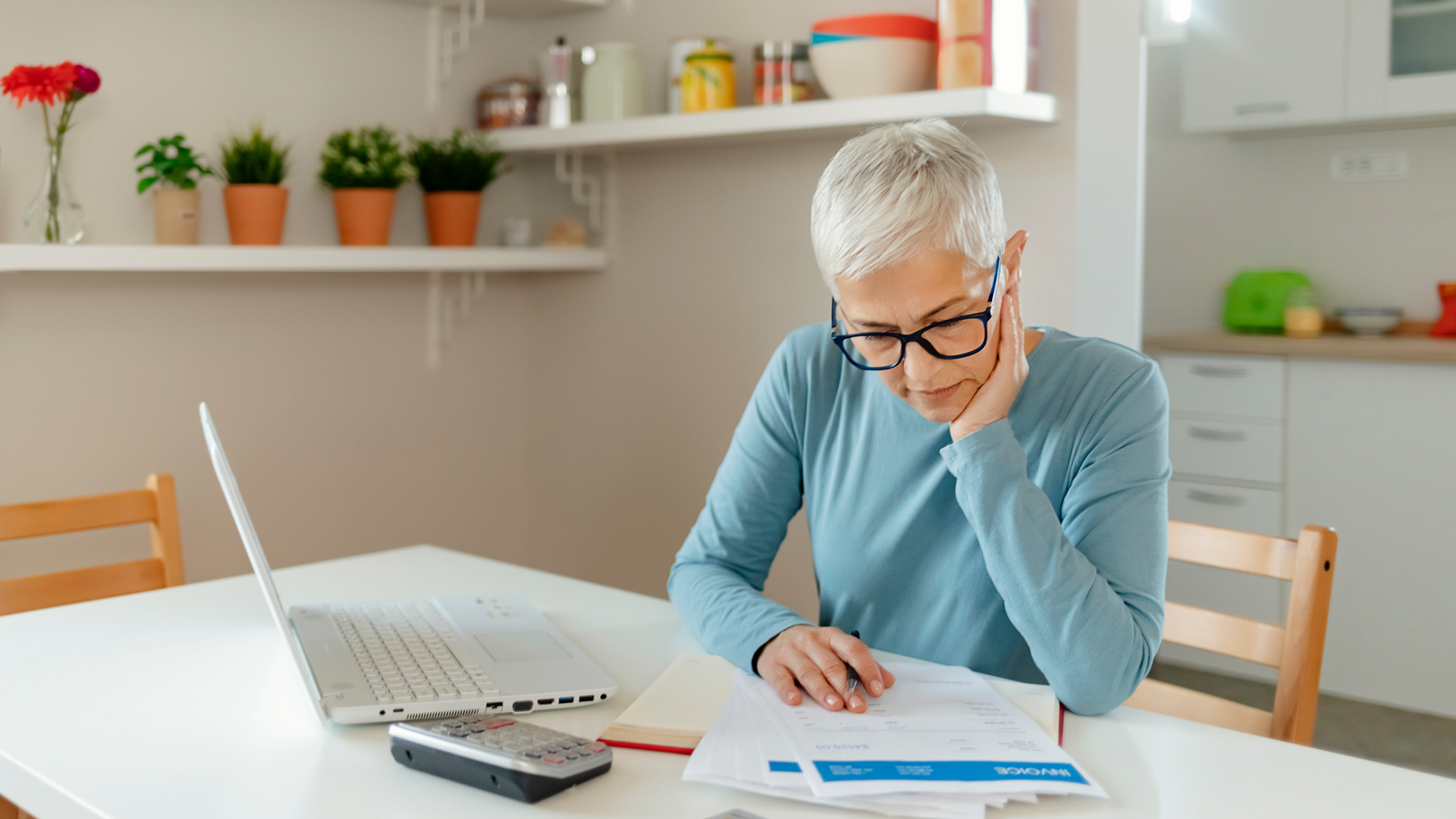